PalletMach helped a 40-year-old factory in Thailand achieve a miraculous turnaround!
In today’s fast-evolving global logistics landscape, the demand for high-quality plastic pallets is surging. Traditional injection-molded pallets, though widely used, are increasingly facing competition from more efficient and cost-effective molded plastic pallets. This shift in demand is prompting more and more manufacturers, both domestic and international, to turn to PalletMach, a leader in plastic recycling and molding solutions.
A Leading Manufacturer in Thailand Faces a Major Challenge
A well-established enterprise in Thailand, with over 40 years of experience in plastic product manufacturing, had been facing a significant challenge as it expanded its operations. This company, known for producing plastic buckets, injection-molded pallets, plastic basins, and plastic chairs, encountered a mountain of waste materials as a byproduct of production. These excess materials caused their old manual injection molding machines to break down completely. Faced with rising costs and inefficiency, the company knew it needed a game-changing solution.
Upon discovering PalletMach's Recycling and Molding Solutions for Waste Plastics, the company was immediately impressed. In May of this year, the customer visited PalletMach’s factory for an in-depth inspection, eager to partner with the company to unlock higher efficiency at a lower cost.
The Power of PalletMach's Compression Molding Technology
PalletMach’s plastic pallet press machine, which employs advanced compression molding technology, offers significant advantages over traditional methods. Here’s how it addresses the challenges faced by the Thai manufacturer:
1. Turning Waste Into Valuable Raw Materials
The waste plastics that had been plaguing the customer—PP, PE, and PVC—are no longer a burden. These materials are the ideal raw materials for PalletMach’s compression molding equipment. From plastic films and broken mulch films to old cable sheaths, plastic bags, and even paper mill scraps, almost any type of waste plastic can be effectively transformed into high-quality products through the compression molding process.
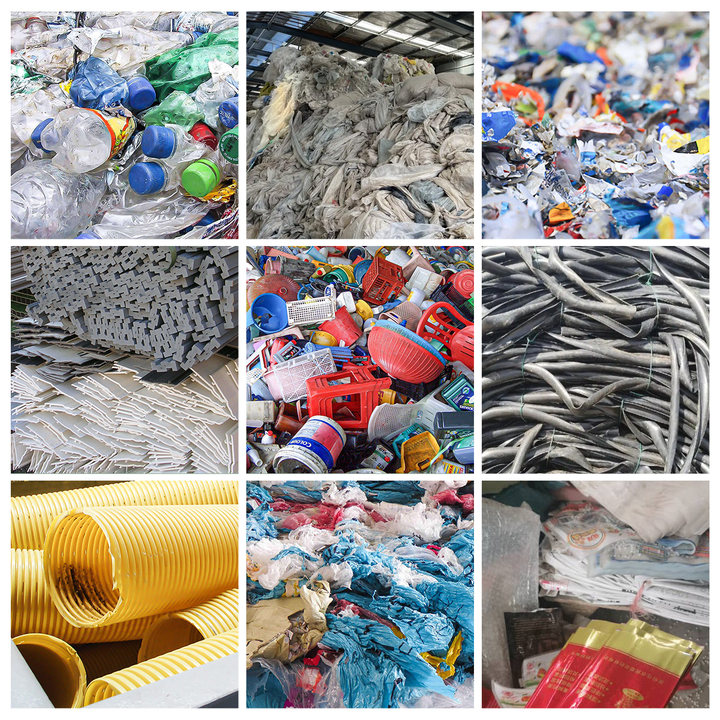
2. No Need for Granulation: Lower Costs, Higher Efficiency
One of the most significant pain points for traditional injection molding is the costly and time-consuming granulation process. Cleaning, filtering, and granulating waste plastics add substantial costs to the production process. With PalletMach’s solution, manufacturers can skip this complicated process. By simply crushing waste plastics and directly feeding them into the machine, production costs are drastically reduced. Not only that, but energy consumption is cut in half, with no wastewater or impurities involved—resulting in truly green manufacturing.
3. Smart, Automated Factory: Precision at Its Best
PalletMach’s proprietary PLC control system ensures that the entire production process is fully automated, requiring minimal human intervention. This leads to increased production accuracy and stability. The automated nature of the system boosts overall operational efficiency, allowing manufacturers to focus on growing their business rather than managing day-to-day production.
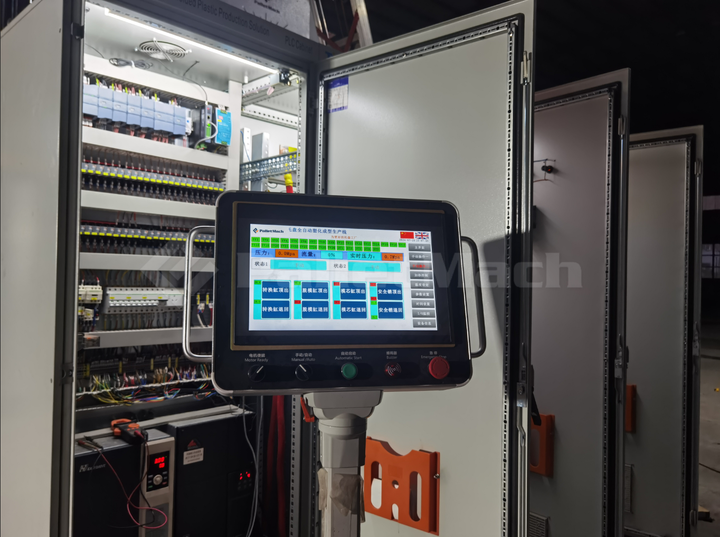
4. Cost-Effective Production: Every Penny Counts
With PalletMach’s technology, raw material costs plummet. Waste plastics are converted into valuable raw materials, significantly reducing raw material expenses. Labor efficiency also skyrockets, as the automated production lines replace the need for manual labor, resulting in higher productivity and lower operating costs.
Injection-molded pallets VS compression-molded plastic pallets
Injection-Molded Pallets: Typically made from expensive, new high-density materials like PP and PE. These pallets offer strong load-bearing capabilities but come with a hefty price tag.
compression-molded plastic pallets: By utilizing waste plastics directly, these pallets offer similar strength and load-bearing capacity at a fraction of the cost. The price advantage is clear, making molded plastic pallets a more affordable and eco-friendly alternative.
Versatility Across Industries
PalletMach’s compression molding equipment is incredibly versatile. It’s not just limited to the production of pallets—other products such as plastic buckets, basins, chairs, turnover boxes, and even manhole covers can be easily produced with the same equipment. This flexibility allows manufacturers to diversify their product offerings and tap into multiple industries without the need for specialized machinery for each product type.
Continuous Innovation: Upgraded Solutions for Superior Results
PalletMach is committed to continually improving its solutions. In response to the customer's concern about uneven raw material melting, PalletMach upgraded its extrusion system from a single-stage extrusion process to a double-stage extrusion process. This upgrade ensures that the raw materials are refined twice, resulting in smoother, more consistent quality. As a result, production efficiency and product quality have both improved significantly.
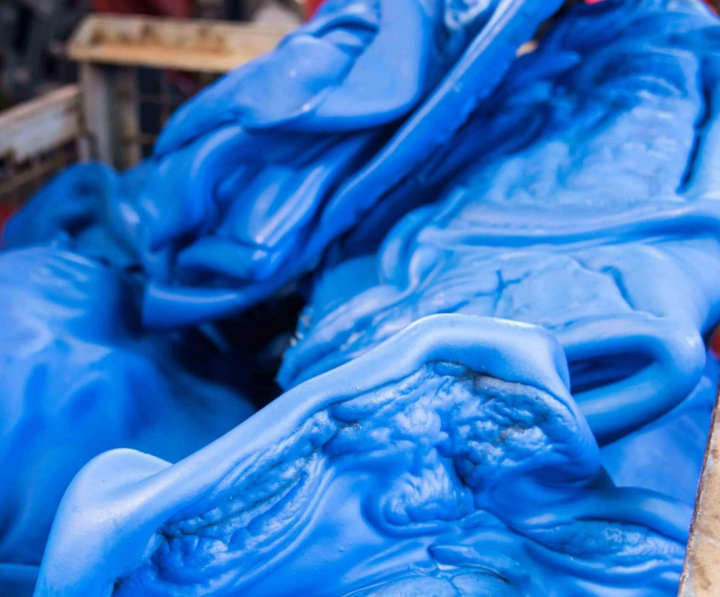
A Resounding Success
The customer was so impressed with PalletMach’s comprehensive solution that they gave a thumbs-up on the spot: “Professional! This solution is amazing!”
A Leading Manufacturer in Thailand Faces a Major Challenge
A well-established enterprise in Thailand, with over 40 years of experience in plastic product manufacturing, had been facing a significant challenge as it expanded its operations. This company, known for producing plastic buckets, injection-molded pallets, plastic basins, and plastic chairs, encountered a mountain of waste materials as a byproduct of production. These excess materials caused their old manual injection molding machines to break down completely. Faced with rising costs and inefficiency, the company knew it needed a game-changing solution.
Upon discovering PalletMach's Recycling and Molding Solutions for Waste Plastics, the company was immediately impressed. In May of this year, the customer visited PalletMach’s factory for an in-depth inspection, eager to partner with the company to unlock higher efficiency at a lower cost.
The Power of PalletMach's Compression Molding Technology
PalletMach’s plastic pallet press machine, which employs advanced compression molding technology, offers significant advantages over traditional methods. Here’s how it addresses the challenges faced by the Thai manufacturer:
1. Turning Waste Into Valuable Raw Materials
The waste plastics that had been plaguing the customer—PP, PE, and PVC—are no longer a burden. These materials are the ideal raw materials for PalletMach’s compression molding equipment. From plastic films and broken mulch films to old cable sheaths, plastic bags, and even paper mill scraps, almost any type of waste plastic can be effectively transformed into high-quality products through the compression molding process.
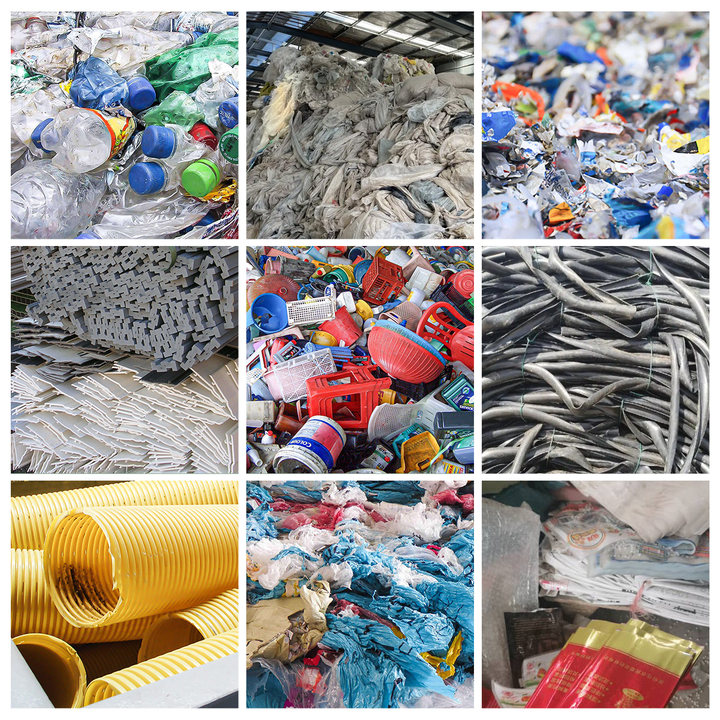
2. No Need for Granulation: Lower Costs, Higher Efficiency
One of the most significant pain points for traditional injection molding is the costly and time-consuming granulation process. Cleaning, filtering, and granulating waste plastics add substantial costs to the production process. With PalletMach’s solution, manufacturers can skip this complicated process. By simply crushing waste plastics and directly feeding them into the machine, production costs are drastically reduced. Not only that, but energy consumption is cut in half, with no wastewater or impurities involved—resulting in truly green manufacturing.
3. Smart, Automated Factory: Precision at Its Best
PalletMach’s proprietary PLC control system ensures that the entire production process is fully automated, requiring minimal human intervention. This leads to increased production accuracy and stability. The automated nature of the system boosts overall operational efficiency, allowing manufacturers to focus on growing their business rather than managing day-to-day production.
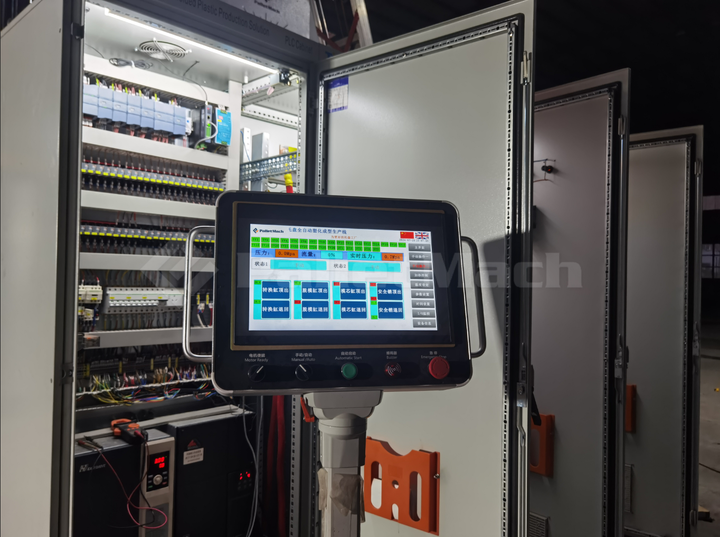
4. Cost-Effective Production: Every Penny Counts
With PalletMach’s technology, raw material costs plummet. Waste plastics are converted into valuable raw materials, significantly reducing raw material expenses. Labor efficiency also skyrockets, as the automated production lines replace the need for manual labor, resulting in higher productivity and lower operating costs.
Injection-molded pallets VS compression-molded plastic pallets
Injection-Molded Pallets: Typically made from expensive, new high-density materials like PP and PE. These pallets offer strong load-bearing capabilities but come with a hefty price tag.
compression-molded plastic pallets: By utilizing waste plastics directly, these pallets offer similar strength and load-bearing capacity at a fraction of the cost. The price advantage is clear, making molded plastic pallets a more affordable and eco-friendly alternative.
Versatility Across Industries
PalletMach’s compression molding equipment is incredibly versatile. It’s not just limited to the production of pallets—other products such as plastic buckets, basins, chairs, turnover boxes, and even manhole covers can be easily produced with the same equipment. This flexibility allows manufacturers to diversify their product offerings and tap into multiple industries without the need for specialized machinery for each product type.
Continuous Innovation: Upgraded Solutions for Superior Results
PalletMach is committed to continually improving its solutions. In response to the customer's concern about uneven raw material melting, PalletMach upgraded its extrusion system from a single-stage extrusion process to a double-stage extrusion process. This upgrade ensures that the raw materials are refined twice, resulting in smoother, more consistent quality. As a result, production efficiency and product quality have both improved significantly.
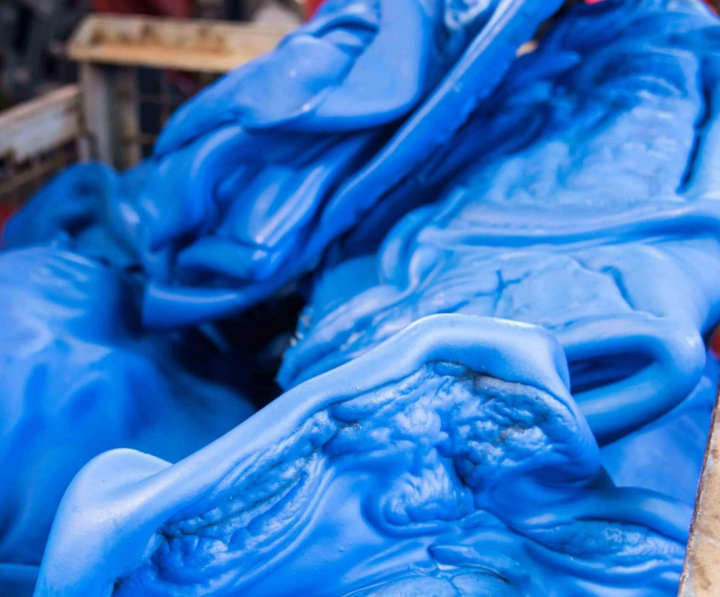
A Resounding Success
The customer was so impressed with PalletMach’s comprehensive solution that they gave a thumbs-up on the spot: “Professional! This solution is amazing!”