PalletMach Conquers North American Market with 6-Ton Static Load Presswood Pallets!
Driven by growing corporate demands for cost control and sustainable development, the press wood pallet industry is experiencing explosive growth, revealing significant blue ocean potential in multiple regions globally.
A Canadian construction industry giant, leveraging its sharp commercial acumen, has emerged as a pioneer in exploring this blue ocean. The client possesses extensive industry experience, robust capabilities in industrial integration and market expansion, and is highly confident about entering the pallet production and sales sector. Its prime location near industrial parks further ensures stable local demand.
Previously hindered by incomplete market information, the client struggled to find an ideal partner in the US. The company's leadership personally visited the PalletMach’s factory for an inspection and decided to procure our "champion equipment" – the press pallet machine and complete production line!
As a seasoned "tech enthusiast," the client's leader focused on three core concerns:
1. How to balance cost and quality?
Unfussy Raw Materials: PalletMach equipment has minimal material requirements! Sawmill waste, wood shavings, bagasse, miscanthus, bamboo, cotton stalks... virtually any renewable plant fiber can be transformed from waste into valuable resources, significantly reducing raw material costs!
Impressively Tough Quality:
PalletMach’s press wood pallets boast a dynamic load capacity of 1.5 tons and a static load capacity of up to 6 tons!
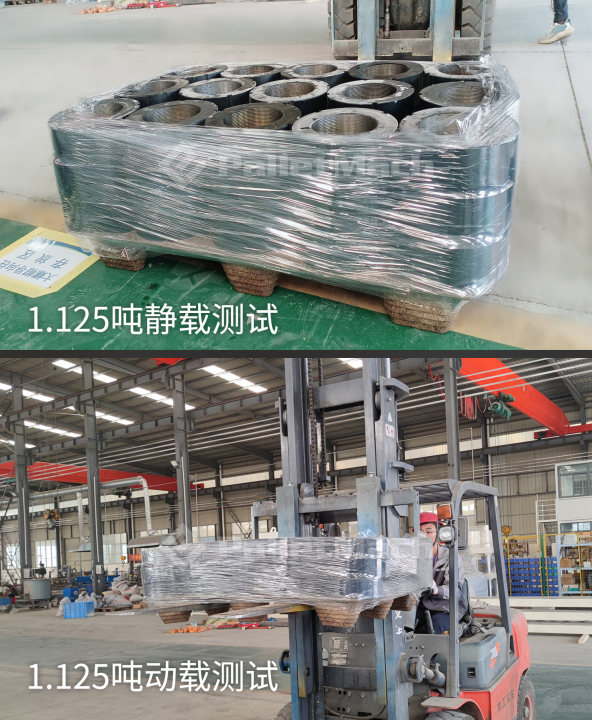
After 42 hours of water immersion, the pallets show no cracks and maintain their dynamic and static load capacities!
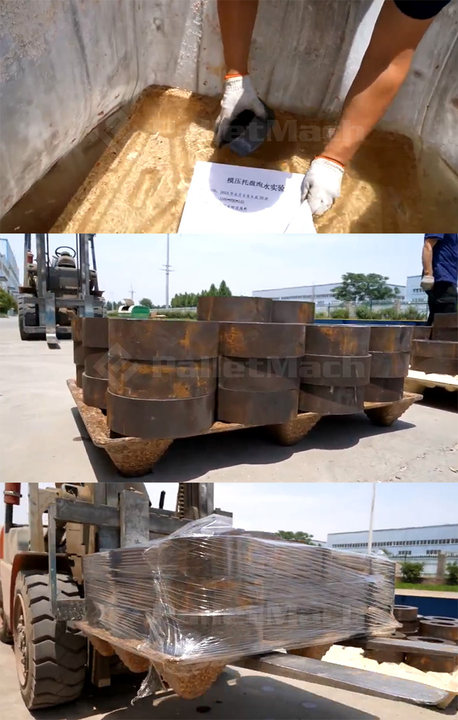
Dragged several meters carrying 1.7 tons, the pallet bottom remained completely intact!
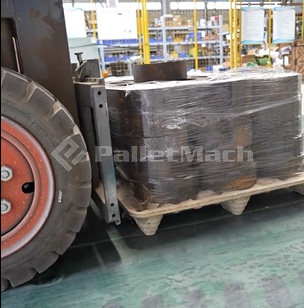
Overall strength meets or exceeds standard pallet specifications!
2. Can It Meet Surging Demand?
Stable Core: PalletMach's press pallet machine features a unique three-beam, four-column structure ensuring precise mold closure and producing smooth, burr-free pallets.
Fully Automated: Integrated with 8 key automation technologies – automatic metering & feeding, glue mixing, discharging, material transfer, leveling, pressing, extraction, and palletizing – enabling truly efficient 24/7 uninterrupted production!
3. Future Development & Support: Is There Assurance?
Forward-Looking Design: PalletMach equipment offers exceptional scalability and flexibility, allowing seamless upgrades to match business growth and meet long-term development needs.
Professional Support: Our engineers proactively clarified technical solutions and addressed energy consumption concerns, providing clear and comprehensive answers.
Thoughtful Customization: Addressing Canada's harsh winters (heavy snow, deep accumulation), our team innovatively modified the original M-shaped parallel roof line design to a T-shape. This effectively prevents snow buildup and ice dam formation, eliminating safety hazards!
Following the client's required pallet styles and dimensions, we produced and shipped a batch of custom samples to Canada. The client was highly satisfied upon receiving them!
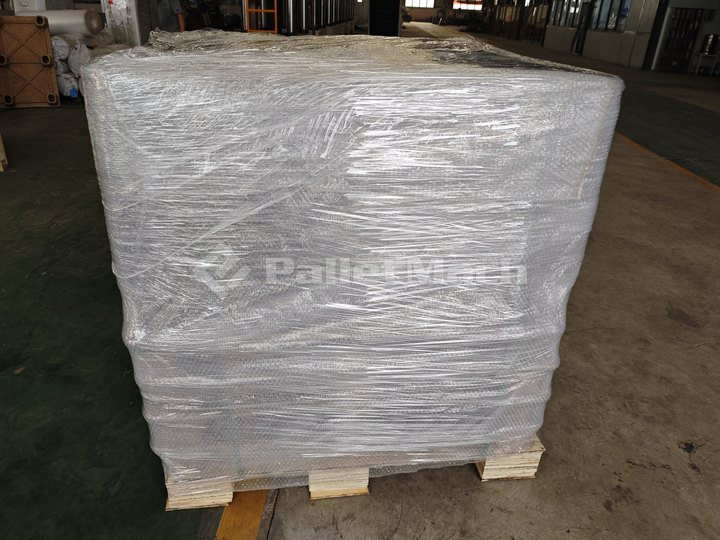
Originally planning to purchase 4 presses, the client ultimately expanded their order to 6 presses. They also procured a comprehensive suite of equipment, including a chipper, twin-shaft feeder, grinder, dryer, bucket elevator, glue mixing system, integrated leveling & molding equipment, and palletizing robots – configuring a complete, end-to-end production line.
A Canadian construction industry giant, leveraging its sharp commercial acumen, has emerged as a pioneer in exploring this blue ocean. The client possesses extensive industry experience, robust capabilities in industrial integration and market expansion, and is highly confident about entering the pallet production and sales sector. Its prime location near industrial parks further ensures stable local demand.
Previously hindered by incomplete market information, the client struggled to find an ideal partner in the US. The company's leadership personally visited the PalletMach’s factory for an inspection and decided to procure our "champion equipment" – the press pallet machine and complete production line!
As a seasoned "tech enthusiast," the client's leader focused on three core concerns:
1. How to balance cost and quality?
Unfussy Raw Materials: PalletMach equipment has minimal material requirements! Sawmill waste, wood shavings, bagasse, miscanthus, bamboo, cotton stalks... virtually any renewable plant fiber can be transformed from waste into valuable resources, significantly reducing raw material costs!
Impressively Tough Quality:
PalletMach’s press wood pallets boast a dynamic load capacity of 1.5 tons and a static load capacity of up to 6 tons!
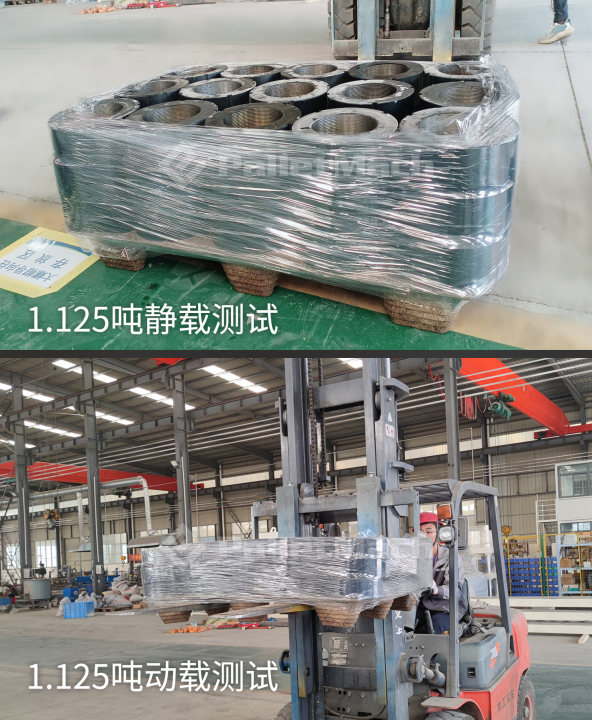
After 42 hours of water immersion, the pallets show no cracks and maintain their dynamic and static load capacities!
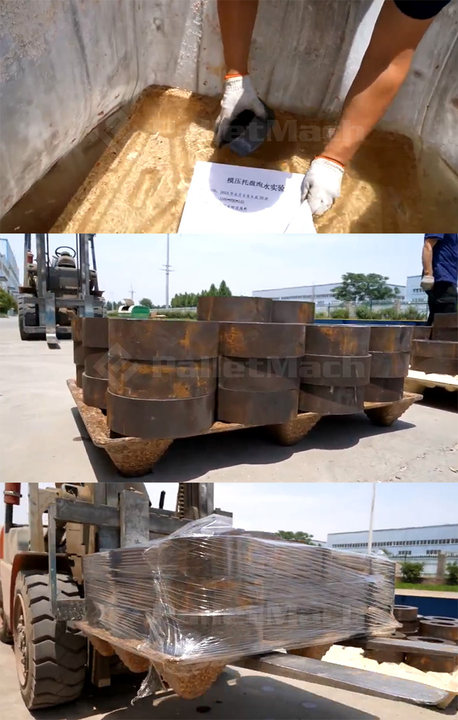
Dragged several meters carrying 1.7 tons, the pallet bottom remained completely intact!
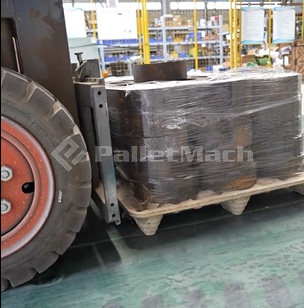
Overall strength meets or exceeds standard pallet specifications!
2. Can It Meet Surging Demand?
Stable Core: PalletMach's press pallet machine features a unique three-beam, four-column structure ensuring precise mold closure and producing smooth, burr-free pallets.
Fully Automated: Integrated with 8 key automation technologies – automatic metering & feeding, glue mixing, discharging, material transfer, leveling, pressing, extraction, and palletizing – enabling truly efficient 24/7 uninterrupted production!
3. Future Development & Support: Is There Assurance?
Forward-Looking Design: PalletMach equipment offers exceptional scalability and flexibility, allowing seamless upgrades to match business growth and meet long-term development needs.
Professional Support: Our engineers proactively clarified technical solutions and addressed energy consumption concerns, providing clear and comprehensive answers.
Thoughtful Customization: Addressing Canada's harsh winters (heavy snow, deep accumulation), our team innovatively modified the original M-shaped parallel roof line design to a T-shape. This effectively prevents snow buildup and ice dam formation, eliminating safety hazards!
Following the client's required pallet styles and dimensions, we produced and shipped a batch of custom samples to Canada. The client was highly satisfied upon receiving them!
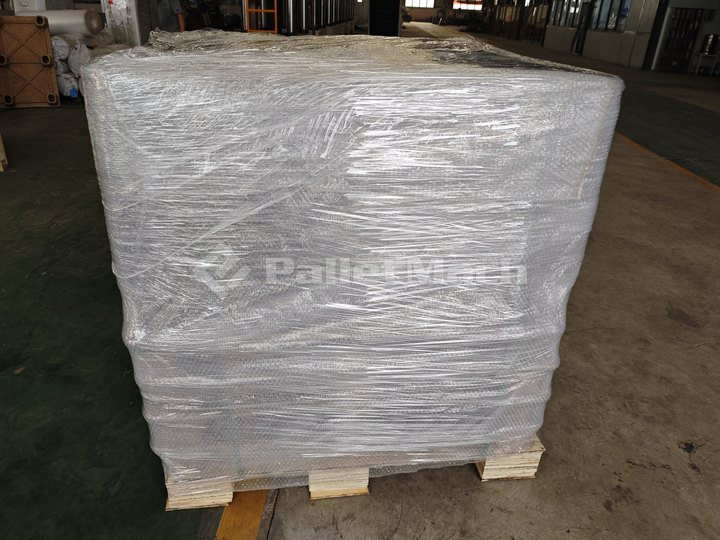
Originally planning to purchase 4 presses, the client ultimately expanded their order to 6 presses. They also procured a comprehensive suite of equipment, including a chipper, twin-shaft feeder, grinder, dryer, bucket elevator, glue mixing system, integrated leveling & molding equipment, and palletizing robots – configuring a complete, end-to-end production line.