PalletMach After-Sale Service of Pallet Production Line in Tunisia
Time: from 25th June 2019 to 1st July 2019
Subject: Summary of business trip to Tunisia
After-Sales Task: to solve the problem of our Tunisian customers’ rotary drum dryer
Person in charge: Overseas business manager
Mr. Liu, vice president of technical engineer
We had checked the rotary drum dryer, one of main machines in pallet block production line, once arrived at our Tunisian customer’s factory immediately.
Engineer Liu learned about the fire from the workers and managers, and then carefully checked the furnace heating system, material delivery system and hot air system of rotary drum dryer. After careful inspection, it was found that the rotary drum dryer induced draft fan noise, and the lack of air volume. We opened the induced draft fan with workers, then we found a large amount of burned material adhered to the surface of the fan impeller after opened the induced draft fan.
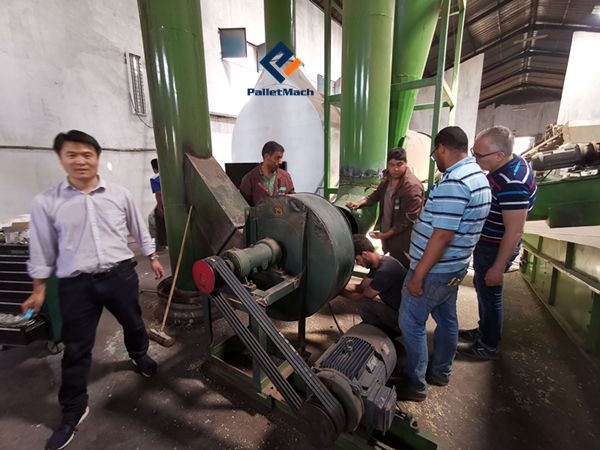
This was the important reason for the fire, which that leaded to the loss of dynamic equilibrium when the fan is working, resulting the noise and insufficient air flow.
After showing the worker how to clean the induced draft fan impeller, the workers quickly cleaned and tested rotary drum dryer. Test results show that the noise reduction, and the air flow returned to normal.
After the air flow returned to normal, Engineer Liu found that the drying materials were wood shavings and wood chips. Because the volume of wood shavings is large and light, it is easy to be drawn out of the chimney, resulting in material gushing to the roof, in the dryer inside the lack of air flow. So we immediately began to solve this problem, equipped with the wind shelter cover in the discharge spiral part and sealed well.
After a thorough inspection of the other parts of rotary drum dryer, there were no abnormal conditions. And then we decided the overall test of rotary drum dryer. After tested rotary drum dryer, the wood dryer run well even drying the lighter wood shavings. However, it was found that the operation of the workers is very irregular, especially in the shutdown sequence. In particular, in the shutdown sequence, they shut down the dryer but there were still remain the materials in the dryer to stop. Also, they shut down rotary drum dryer before the import and export temperature cooled. All above, there were a great fire risk. It can be concluded that the main cause of the fire is man-made operation, and then the lack of proper maintenance of equipment and the material characteristics.
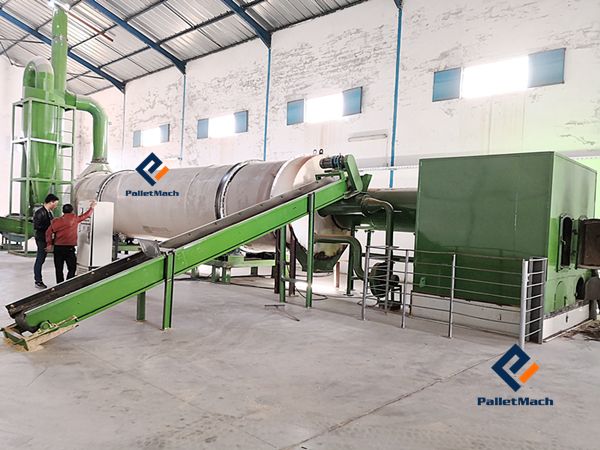
After finding and solving the problem, we continued to run rotary drum dryer for 2 days to expose the problem and fix it as much as possible. Later, through the observation of the operation of workers, it is found that the most important problem is the wrong operation of workers.
From this problem, it also exposed the lack of experience for customers in the factory organization and management of production workers. Hence, we worked with our Tunisian customers to in the dryer workshop to train all workers. We taught workers their functions, correct operation and maintenance methods of the equipment one by one components. And we also guided them the correct operation and operation of equipment startup and shutdown. So as to avoid the similar problems. At the same time, we also assisted our Tunisian customers to establish management system, including induction training, operation designated to one person, and regular maintenance and the work record table.
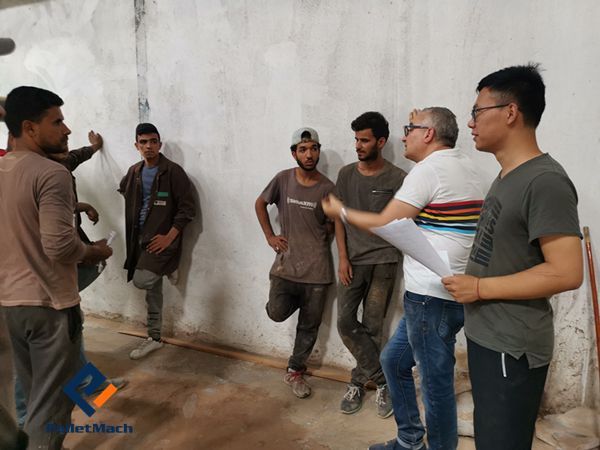
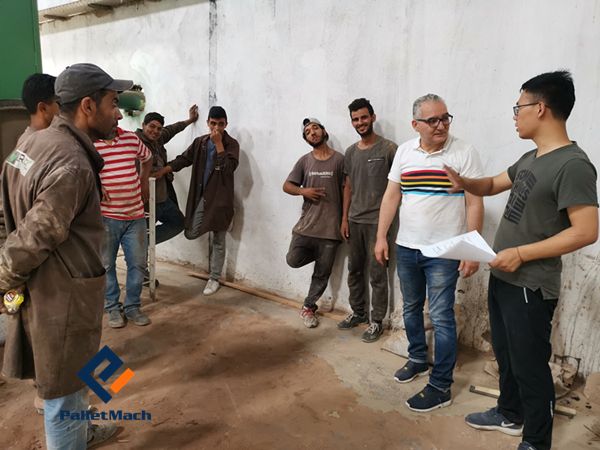
After two days of stable operation of the wood dryer, we have completed the main task of this after-sale service. In accordance with the principle of responsibility, we checked every piece of equipment in our Tunisian customer’s production plant. In addition, we also put forward recommendations and develop management methods to ensure stable production. Hence, our customers were very satisfied with our after-sale service.
Reflection:
1. PalletMach likes to take 101% responsibility.
We do not sell all machines of presswood pallet and pallet block production. Meanwhile, our service includes the plan formulation, the equipment design and the manufacture, the installment, the training, provides the management suggestion and the sales suggestion. So as to guarantee stabilization production for you. Besides, we also help you to produce high quality presswood pallets and pallet blocks, and build your brand.
2. Low Labor costs are not an advantage.
For the operation and maintenance of all equipment, it requires educated workers, which have the sense of responsibility and simple equipment knowledge. Cheap labor means a low level of education, so it prone to the problems of operation and maintenance equipment. Besides, it requires that high automation of all pallet machine, easy to maintain, and simple operation. You are on the high demand for after-sales service, and it is also PalletMach does. And PalletMach ensures after-sales service, equipment design and manufacturing quality.
3. Win-win cooperation
For us, the goal of any business collaboration should be win-win cooperation. After you pay the deposit to us, it means the cooperation officially starts. Before this, we will help you to fully analyze all factors, such as the raw material, the products, the production, the labor, the market and so on. We understand you, also to let you understand US. This is the premise that win-win cooperation can be realized. As a responsible company, PalletMach has a strong sense of responsibility to establish high-quality enterprises, to create value for customers. In addition, we also devote ourselves to create more jobs for more people and promote local pallet industry.

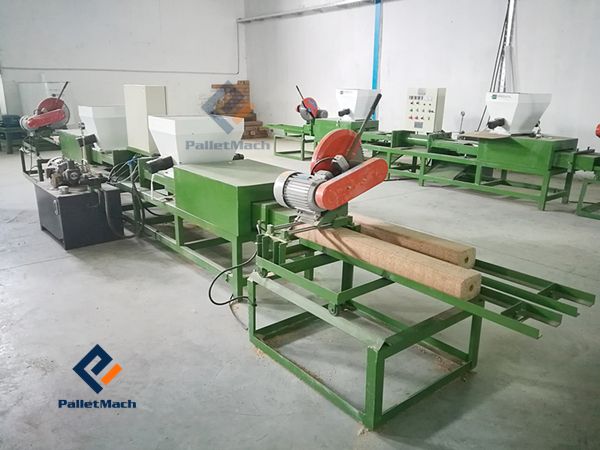
Installation and commissioning service contents
Mainly include several aspects:
1. To guide and draw up the plan of the construction design, installation and commissioning program and time schedule.
2. To guide and organize the installation of pallet machine, and to solve various technical problems.
3. To inspect the quality of pallet machine installation to ensure that it meets the technical standards.
4. To guide pallet machine commissioning, and to handle a variety of anomalies.
5. To guide the running of pallet machine to ensure machine normal operation.
Installation and commissioning service standard
1. PalletMach will send the professional technical staff to provide the clients with installation and commissioning services.
2. PalletMach will ensure the quality of installation and commissioning, so that pallet machine operates well and good quality of final product.
3. PalletMach will provide the clients with installation, operation and maintenance manuals, to reduce the operation and maintenance cost of pallet machine.
Installation and commissioning service program
There are three main steps:
1. Installation and commissioning preparation.
1.1 Check pallet machine, accessories, attachments, tools, drawings and materials.
1.2 Draw up construction design, installation and commissioning programs and appropriate technical measures according to the characteristics and technical requirements of pallet machine installation and commissioning.
2. Installation and commissioning implementation.
2.1 Guide the pallet machine installation and commissioning in strict accordance with the quality requirements and procedures.
2.2 Solve the technical problems of installation and commissioning.
2.3 Inspect the quality of wooden pallet making machine installation and commissioning, to ensure normal operation of pallet machine.
3. Installation and commissioning summary.
3.1 Summarize and evaluate the quality of installation and commissioning.
3.2 Listen to comment and suggestion of the clients to in order to improve product design and manufacturing processes of pallet machine.
PalletMach provides all clients with installation and commissioning service all around the world.
This time, we went to Tunisia to solve the fire of rotary drum dryer. It is the first time, but not the last time. Our professional after-sale service team is already to help all our customers to deal with all problems.
Subject: Summary of business trip to Tunisia
After-Sales Task: to solve the problem of our Tunisian customers’ rotary drum dryer
Person in charge: Overseas business manager
Mr. Liu, vice president of technical engineer
We had checked the rotary drum dryer, one of main machines in pallet block production line, once arrived at our Tunisian customer’s factory immediately.
Engineer Liu learned about the fire from the workers and managers, and then carefully checked the furnace heating system, material delivery system and hot air system of rotary drum dryer. After careful inspection, it was found that the rotary drum dryer induced draft fan noise, and the lack of air volume. We opened the induced draft fan with workers, then we found a large amount of burned material adhered to the surface of the fan impeller after opened the induced draft fan.
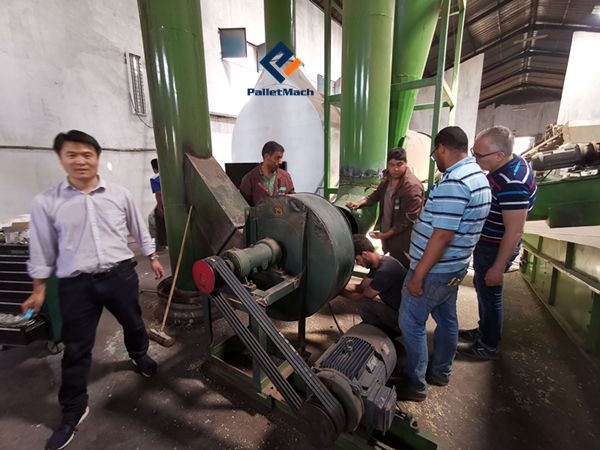
This was the important reason for the fire, which that leaded to the loss of dynamic equilibrium when the fan is working, resulting the noise and insufficient air flow.
After showing the worker how to clean the induced draft fan impeller, the workers quickly cleaned and tested rotary drum dryer. Test results show that the noise reduction, and the air flow returned to normal.
After the air flow returned to normal, Engineer Liu found that the drying materials were wood shavings and wood chips. Because the volume of wood shavings is large and light, it is easy to be drawn out of the chimney, resulting in material gushing to the roof, in the dryer inside the lack of air flow. So we immediately began to solve this problem, equipped with the wind shelter cover in the discharge spiral part and sealed well.
After a thorough inspection of the other parts of rotary drum dryer, there were no abnormal conditions. And then we decided the overall test of rotary drum dryer. After tested rotary drum dryer, the wood dryer run well even drying the lighter wood shavings. However, it was found that the operation of the workers is very irregular, especially in the shutdown sequence. In particular, in the shutdown sequence, they shut down the dryer but there were still remain the materials in the dryer to stop. Also, they shut down rotary drum dryer before the import and export temperature cooled. All above, there were a great fire risk. It can be concluded that the main cause of the fire is man-made operation, and then the lack of proper maintenance of equipment and the material characteristics.
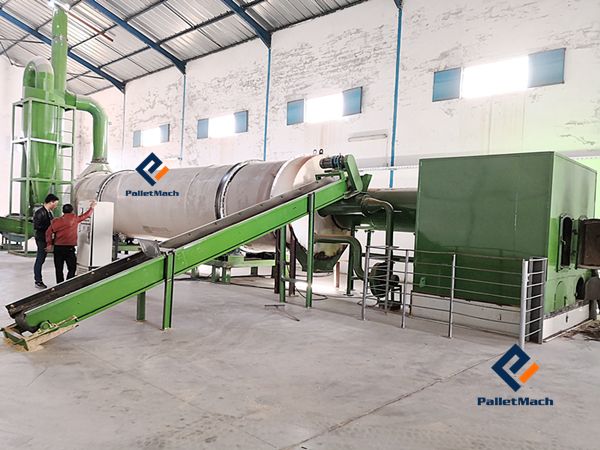
After finding and solving the problem, we continued to run rotary drum dryer for 2 days to expose the problem and fix it as much as possible. Later, through the observation of the operation of workers, it is found that the most important problem is the wrong operation of workers.
From this problem, it also exposed the lack of experience for customers in the factory organization and management of production workers. Hence, we worked with our Tunisian customers to in the dryer workshop to train all workers. We taught workers their functions, correct operation and maintenance methods of the equipment one by one components. And we also guided them the correct operation and operation of equipment startup and shutdown. So as to avoid the similar problems. At the same time, we also assisted our Tunisian customers to establish management system, including induction training, operation designated to one person, and regular maintenance and the work record table.
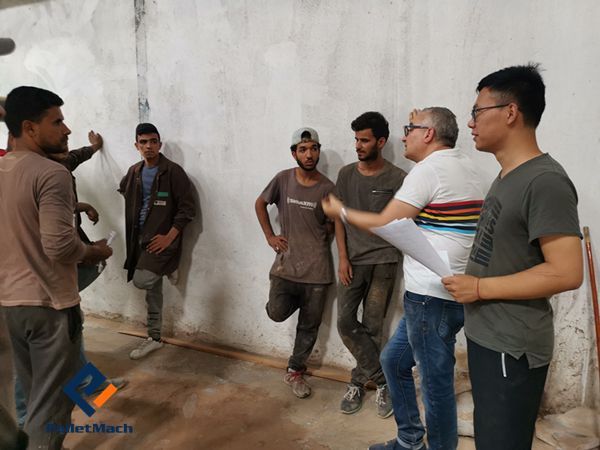
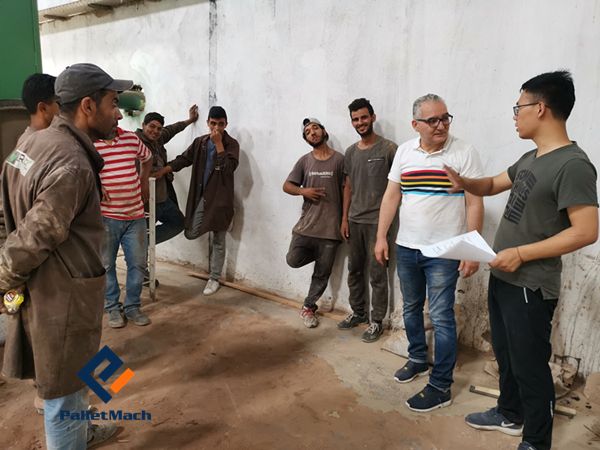
After two days of stable operation of the wood dryer, we have completed the main task of this after-sale service. In accordance with the principle of responsibility, we checked every piece of equipment in our Tunisian customer’s production plant. In addition, we also put forward recommendations and develop management methods to ensure stable production. Hence, our customers were very satisfied with our after-sale service.
Reflection:
1. PalletMach likes to take 101% responsibility.
We do not sell all machines of presswood pallet and pallet block production. Meanwhile, our service includes the plan formulation, the equipment design and the manufacture, the installment, the training, provides the management suggestion and the sales suggestion. So as to guarantee stabilization production for you. Besides, we also help you to produce high quality presswood pallets and pallet blocks, and build your brand.
2. Low Labor costs are not an advantage.
For the operation and maintenance of all equipment, it requires educated workers, which have the sense of responsibility and simple equipment knowledge. Cheap labor means a low level of education, so it prone to the problems of operation and maintenance equipment. Besides, it requires that high automation of all pallet machine, easy to maintain, and simple operation. You are on the high demand for after-sales service, and it is also PalletMach does. And PalletMach ensures after-sales service, equipment design and manufacturing quality.
3. Win-win cooperation
For us, the goal of any business collaboration should be win-win cooperation. After you pay the deposit to us, it means the cooperation officially starts. Before this, we will help you to fully analyze all factors, such as the raw material, the products, the production, the labor, the market and so on. We understand you, also to let you understand US. This is the premise that win-win cooperation can be realized. As a responsible company, PalletMach has a strong sense of responsibility to establish high-quality enterprises, to create value for customers. In addition, we also devote ourselves to create more jobs for more people and promote local pallet industry.

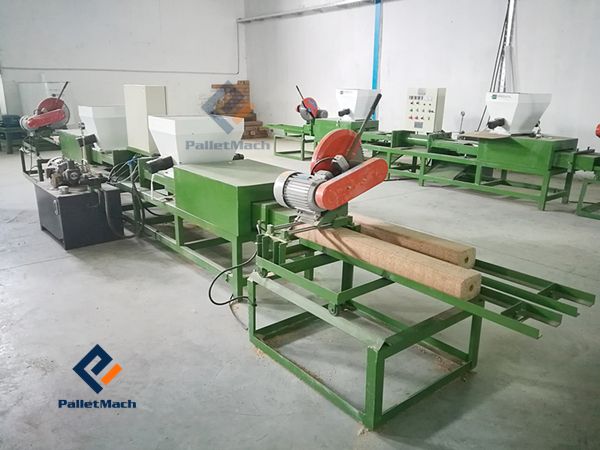
Installation and commissioning service contents
Mainly include several aspects:
1. To guide and draw up the plan of the construction design, installation and commissioning program and time schedule.
2. To guide and organize the installation of pallet machine, and to solve various technical problems.
3. To inspect the quality of pallet machine installation to ensure that it meets the technical standards.
4. To guide pallet machine commissioning, and to handle a variety of anomalies.
5. To guide the running of pallet machine to ensure machine normal operation.
Installation and commissioning service standard
1. PalletMach will send the professional technical staff to provide the clients with installation and commissioning services.
2. PalletMach will ensure the quality of installation and commissioning, so that pallet machine operates well and good quality of final product.
3. PalletMach will provide the clients with installation, operation and maintenance manuals, to reduce the operation and maintenance cost of pallet machine.
Installation and commissioning service program
There are three main steps:
1. Installation and commissioning preparation.
1.1 Check pallet machine, accessories, attachments, tools, drawings and materials.
1.2 Draw up construction design, installation and commissioning programs and appropriate technical measures according to the characteristics and technical requirements of pallet machine installation and commissioning.
2. Installation and commissioning implementation.
2.1 Guide the pallet machine installation and commissioning in strict accordance with the quality requirements and procedures.
2.2 Solve the technical problems of installation and commissioning.
2.3 Inspect the quality of wooden pallet making machine installation and commissioning, to ensure normal operation of pallet machine.
3. Installation and commissioning summary.
3.1 Summarize and evaluate the quality of installation and commissioning.
3.2 Listen to comment and suggestion of the clients to in order to improve product design and manufacturing processes of pallet machine.
PalletMach provides all clients with installation and commissioning service all around the world.
This time, we went to Tunisia to solve the fire of rotary drum dryer. It is the first time, but not the last time. Our professional after-sale service team is already to help all our customers to deal with all problems.